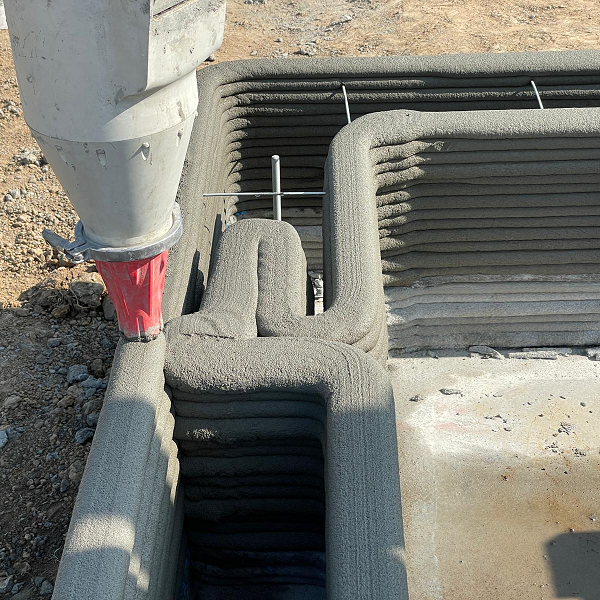
Luyten 3D technology company wins nearly $3 million CRC-P Grant to build affordable housing across outback Australia
World leading Australian 3D printing technology company, Luyten 3D, has been awarded a grant through the federal government’s Cooperative Research Centres Projects Grants program to address the need for affordable and durable housing across outback Australia.
The project which involves Luyten 3D collaborating with the University of New South Wales (UNSW) and Hanson Construction Materials (Hanson) will develop and deliver innovative 3D printed housing solutions to remote parts of Australia to support mining and other communities.
The project will run for several years at a total cost of nearly $6.5 million dollars. The CRC-P program will provide $2,993,626 of grant funding.
“We are absolutely thrilled to be awarded the CRC-P grant for our project. If we as a nation want to address affordability, quality of stock and adequate conditions of housing in Australia’s remote areas, then different manufacturing technologies need to be developed removing logistics as a bottleneck, bringing manufacturing on site, and building with locally sourced zero-carbon/kilometre materials,” Luyten 3D Co-Founder and Global CEO, Ahmed Mahil said.
“It is wonderful that the importance of our project has been embraced by the program. Our project is a response to the needs of the mining sector and communities across outback and remote parts of the country and addresses a critical aspect of the government’s commitment to deliver more homes for Australians utilising technology that is already a focus for construction companies.
“The partnership between Luyten 3D, UNSW and Hanson will involve developing a 3D print system, with hard and software, to build houses faster and cheaper using local materials.”
Luyten 3D’s revolutionary 3D printing technology for the building and construction industry has already been identified as cutting edge by companies across the globe and is in use in the US, Canada, Asia, Europe and the Middle East.
“Luyten 3D is already helping to build affordable housing in the US and now we will be expanding our operations locally to help print affordable housing in outback Australia,” Mahil said.
“The benefit of our technology is that we can transport our 3D printers to locations in remote areas and print using local materials. We are able to create a mix of terracrete, rather than concrete, utilising local ingredients. Not only is this more cost effective, it is also more sustainable as terracrete requires less water than concrete.
“Our Luyten Platypus X12 printer is able to be transported in compact form and unfolded on site to reach a height of six metres and a width of 12 metres enabling it to print virtually any house in one go.
“The CRC-P grant will provide the necessary funding to ensure we have the capability and resources to deliver life-changing houses for communities in remote parts of the country that are affordable, durable and aesthetically compatible with their surrounds.”
Associate Professor, Haeusler, of UNSW said, “The project strongly aligns with the objectives of the ARC Industry Transformation Training Centre for Next-Gen Architectural Manufacturing, which aims to address Australia’s housing crisis through sustainable and digital approaches.
“What excites me the most is that through the CRC-P project, we can extend our efforts to remote and very remote communities, who face additional financial challenges in affording housing due to increased costs of material and labour transportation over vast distances in Australia. Our innovative approach of bringing the factory to the construction site while utilising locally sourced materials will effectively tackle these issues, enabling the construction of custom-designed homes at a more affordable price.”
Luyten’s cutting edge 3D printer technology enables builders to transform construction projects that would traditionally take months or years to complete and instead finish them within a number of days. The 3D concrete printing revolutionary technology reduces 60 percent of construction waste, 70 percent of production time, and 80 percent of labour costs when comparing hands-on construction projects.
“In addition, the technology is proven to increase construction site efficiency with 60 percent guaranteed costs savings, 300 to 500 times shorter execution times, and an 80 percent total reduction in monetary expenses without formwork in concrete construction. The world has never seen capabilities like this before,” Mahil said.
“When forming Luyten, we were cognisant of the construction industry’s carbon footprint, and determined to create construction solutions for generations to come that reduce emissions. Our unmatched technology employs up to 40 percent less carbon dioxide emissions through propriety mixes that reduce use of cement, and the robotic systems reduce construction site and logistics carbon dioxide footprints by 50 to 70 percent.”